社内ものづくりコンテスト『地球ゴマ』
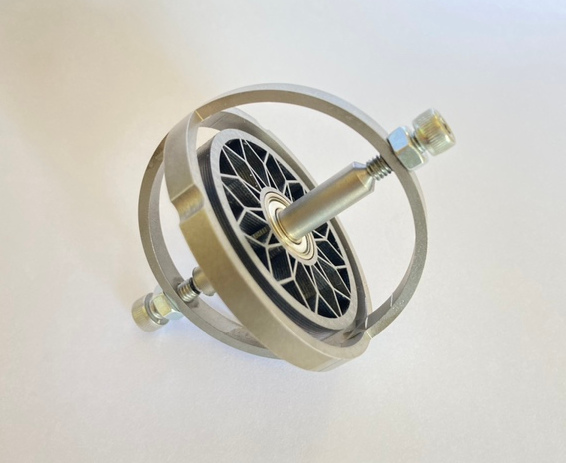
コマチームでは、加工技術向上と力試しの機会になればと考え、第2回目から地球ゴマの制作に着手しました。
地球ゴマの写真を基に、形状・寸法を決定、加工計画を立て、初号機を作り上げました。
初めての地球ゴマの制作にも関わらず、見た目は不格好ながら、自立する状態まで仕上げることが出来ました。
とはいえ、とても市販品と比べると天と地の差。改善点はかなりありそうです。
改善点
①軸ブレを少なくする
②回転抵抗を少なくする
③軽量化
今回の第3回目のコマ制作では、上記に上げた課題をクリアするべく作業を進めたいと思います。
製作過程は、写真を交えお話ししたいと思います。
どうぞお付き合い願います。
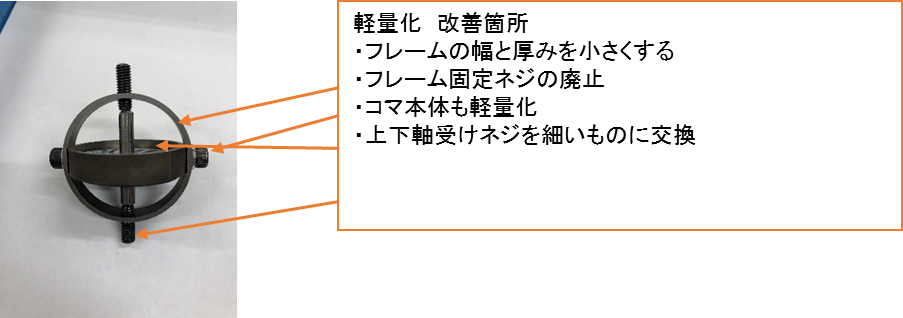

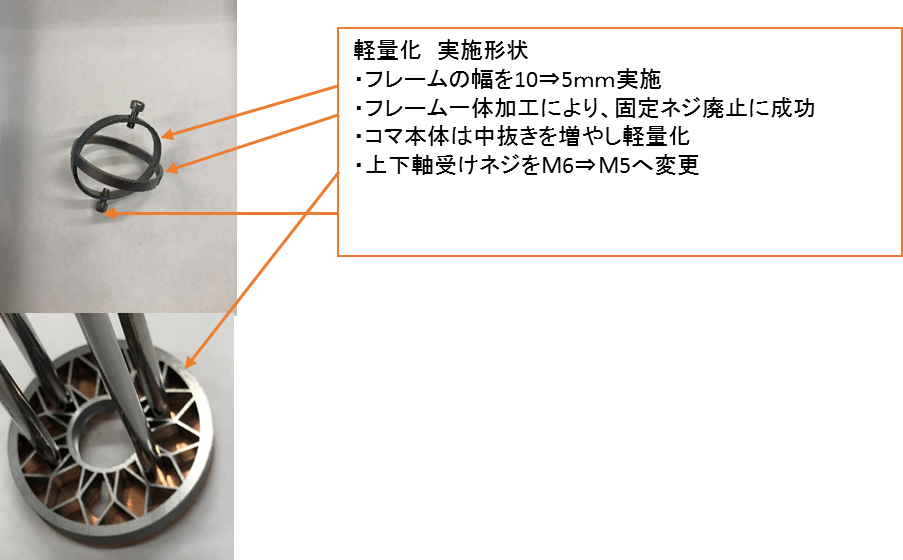
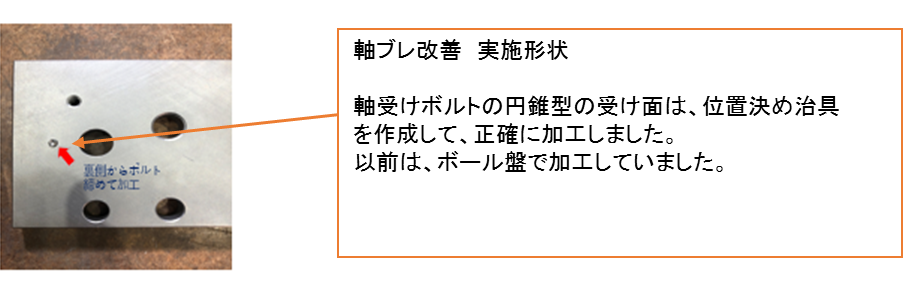
フレーム一体加工
80mm立方体ブロックに前加工を施し、ワイヤー放電加工機で加工。
ブロックをひっくり返しながら四方面を加工。未聞の工程数に驚きです。
加工時間はなんと30時間。段取り時間を含めると新車の原付バイクは買えるほどの加工費になりました。
加工中には、予想もしていない問題が起こります。
工程を進めるほどに、抜けカスが細かく抜け落ち、運悪く加工機の隙間に挟まってしまい、機械部品を破損してしまいました。
通常業務では、経験もしないことが起こり、ものづくりの難しさを痛感。ともに、新たな経験ができ、今後の仕事に役立つ力強い経験値となりました。
加工も楽しく出来ました。
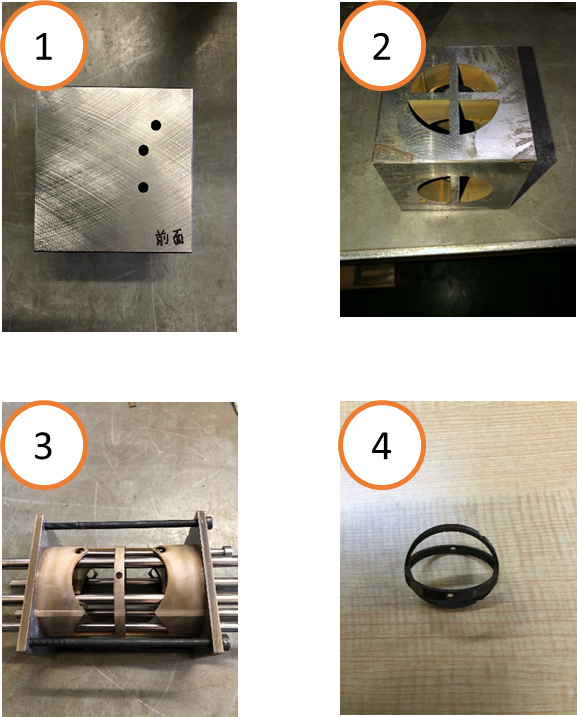
ちょいと寄り道加工
コマ本体の加工は、1枚0.5㎜厚の板から、レーザー切断加工機で作ります。中抜き、内径、外径の順に仕上げています。
加工が終わったシートをバリ取り、積層、レーザー溶接して、コマの仕上がりです。
ちょいと寄り道加工と称し、接着積層のコマを作ります。
接着剤プリコート材料を同様の流れで加工します。
最後の溶接工程えを接着積層工程へ寄り道、電気炉を使い、接着剤を溶かし、冷却して、再硬化させて、一体化させます。
炉に入れるための位置だし治具は簡易的なものを作成しました。
既存の製品治具に、位置決めの為のピンを通す穴をあけただけのプレートを切り出し、ピンを数本立て、簡素に作りました。
積ズレするかと思いましたが、意外にきれいに仕上がりました。
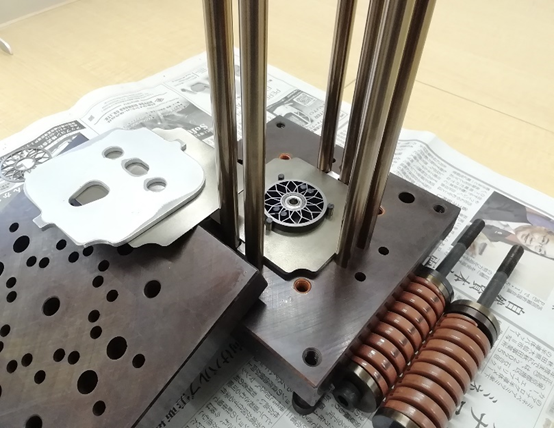