ラミネーション加工
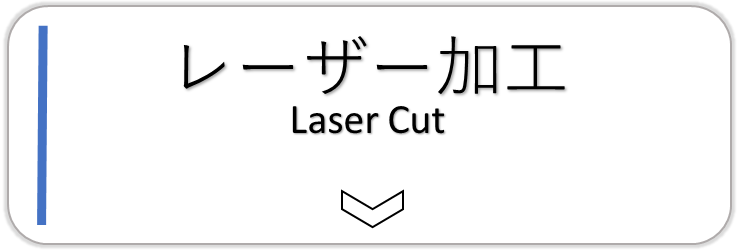
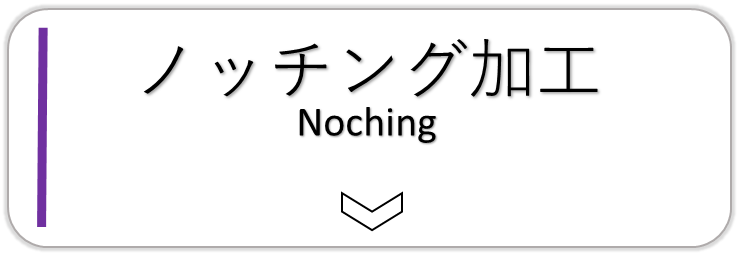

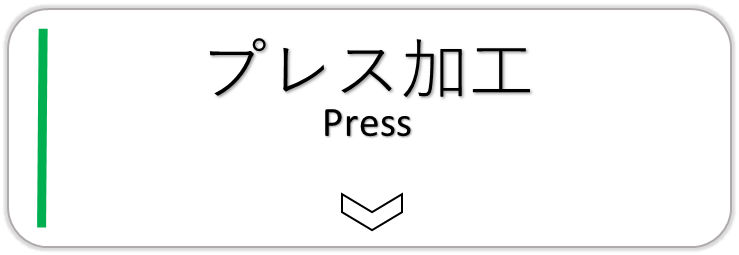
新製品の開発を巡る競争が激化する昨今ですが、開発費には限りがあります。
近年はモーター解析ソフトの活用で試作品の製作台数を減らすことも可能となりましたが、その少量製作の為にプレス用の金型から起こすのはコスト高になりますし、ワイヤー加工では量産品との特性に差が生じるといった事実を耳にします。また、エッチング加工では電磁鋼板の肝である絶縁皮膜を剥がさないと腐食が出来ない等、各加工方法にはそれぞれ一長一短がございます。
弊社では様々な加工方法に対応することで、お客様のニーズに合わせたより良い加工方法にて、高品質・低コストな製品をお届けいたします。
それぞれの加工機の加工可能範囲はこちら
レーザー加工
レーザーによるコア製作
モーターコア加工に特化したレーザー加工機を導入しており、φ0.1の穴加工や微細な形状も加工することが可能です。
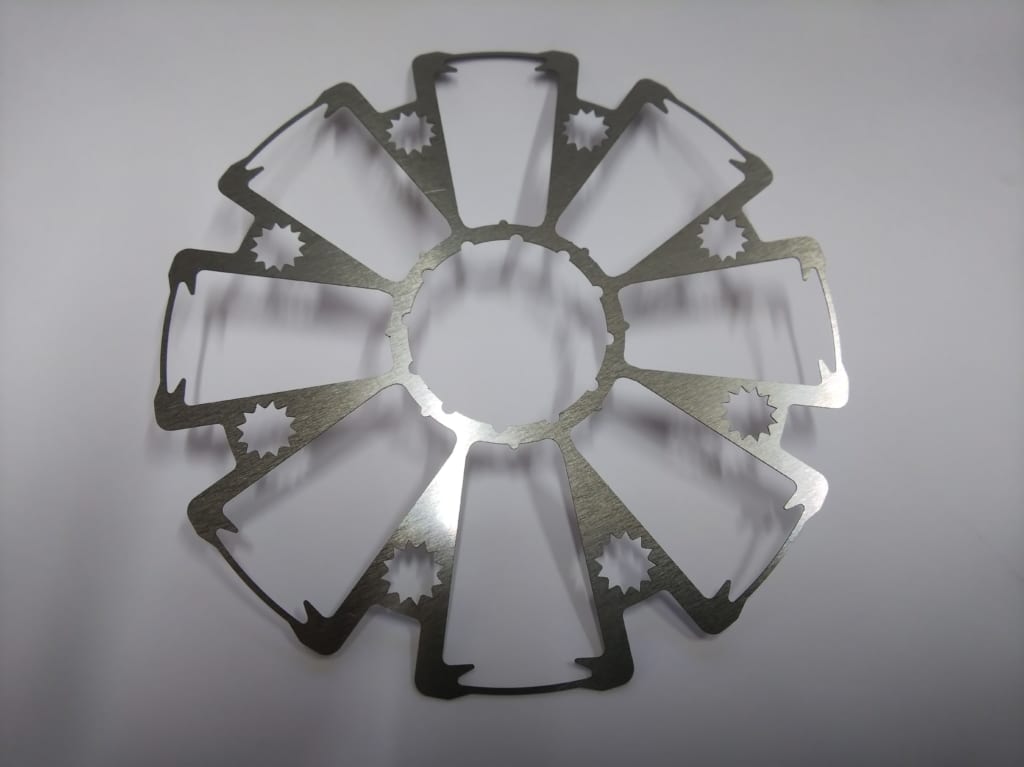
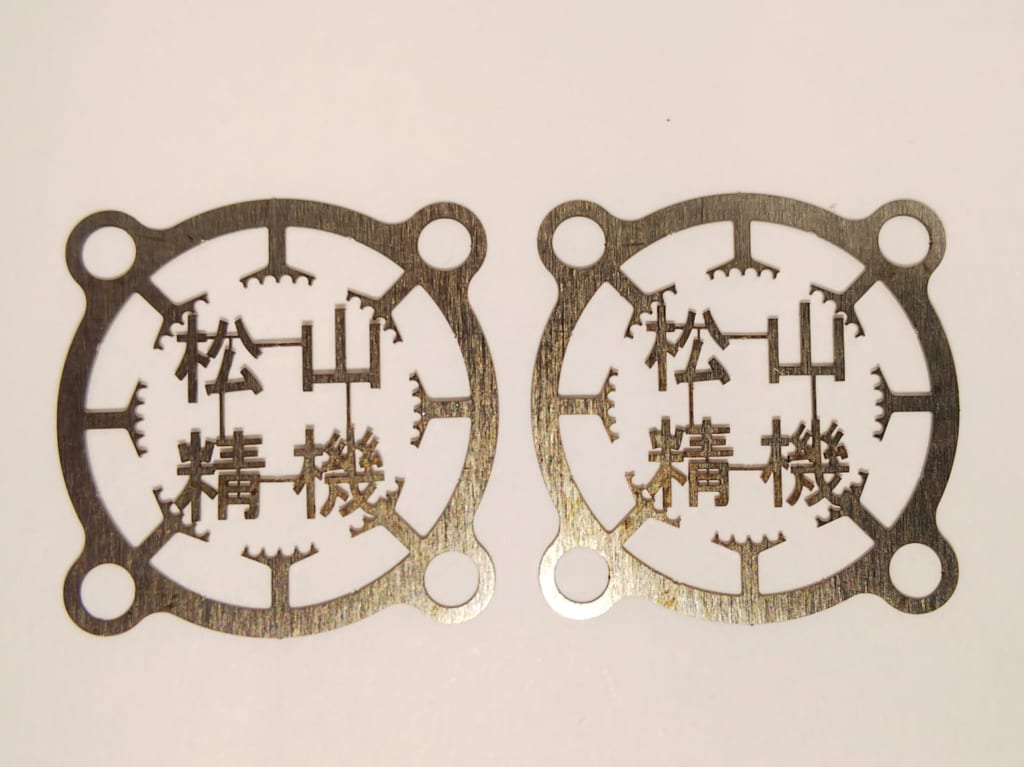
従来のレーザー加工機では苦手とした薄板の電磁鋼板を、プレス加工品並みのコア特性・ワイヤ加工品に近い高精度で加工でき、小ロットでの製作コストはどの加工方法よりも低く抑えられます。
リニア駆動により位置決め精度も信頼できるレーザー加工機+材料搬入出装置による24h無人運転にて、高精度・短納期・コスト削減にお応えします。
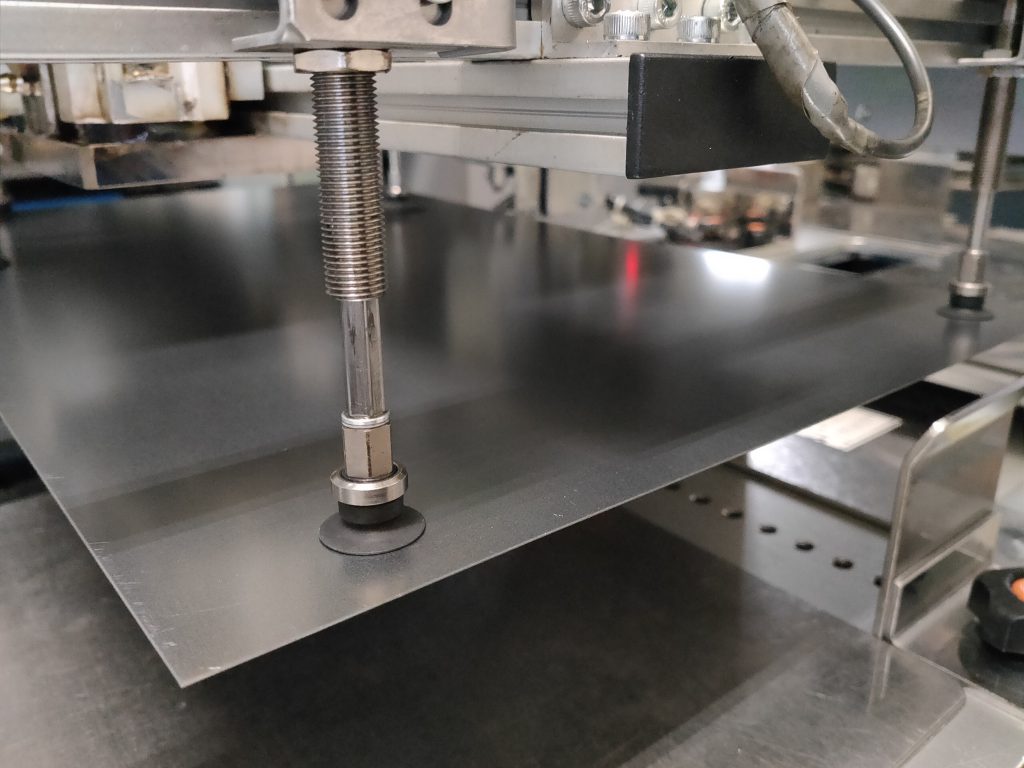
□500×500のテーブルに入る形状であれば微細な形状からφ480程度のコアまで対応可能です。(それ以上の大きさも加工可能です。ご相談ください)
保有材料も0.2~0.5まで(日本製鉄製、JFE製 有)各種取り揃えております。
板厚に関係なく材料搬入出装置にて対応可能です。珪素鋼板以外や、0.5以上の板厚にも対応可能です。ご相談ください。
リニアモーター式のレーザー加工機による高精度加工
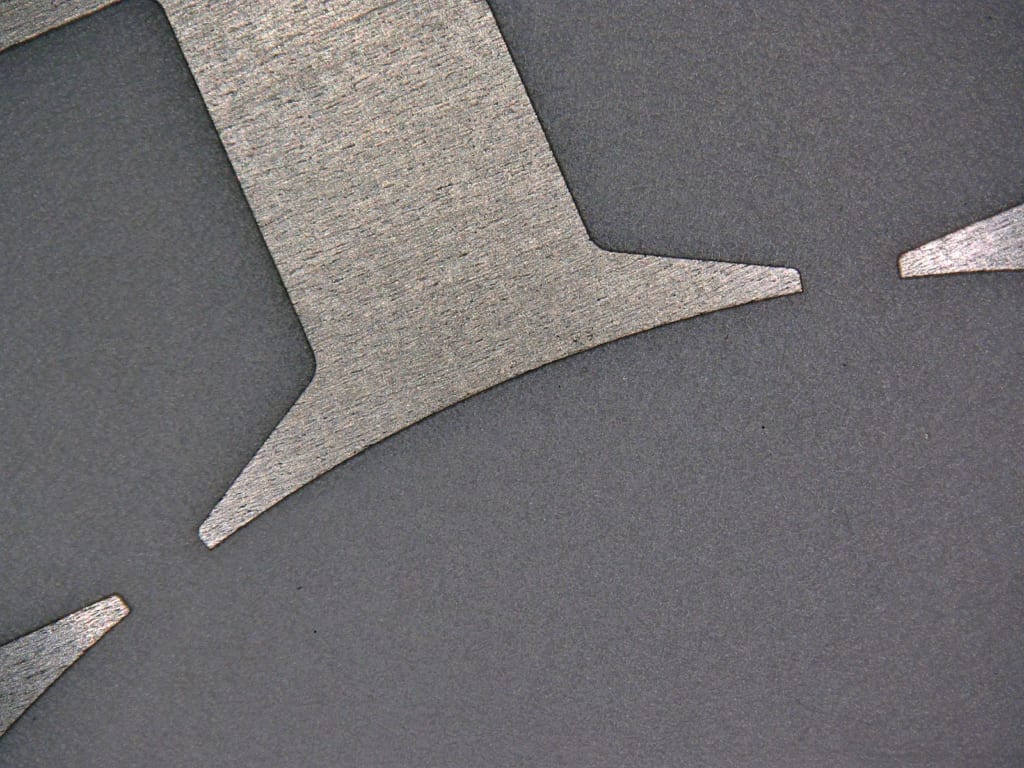
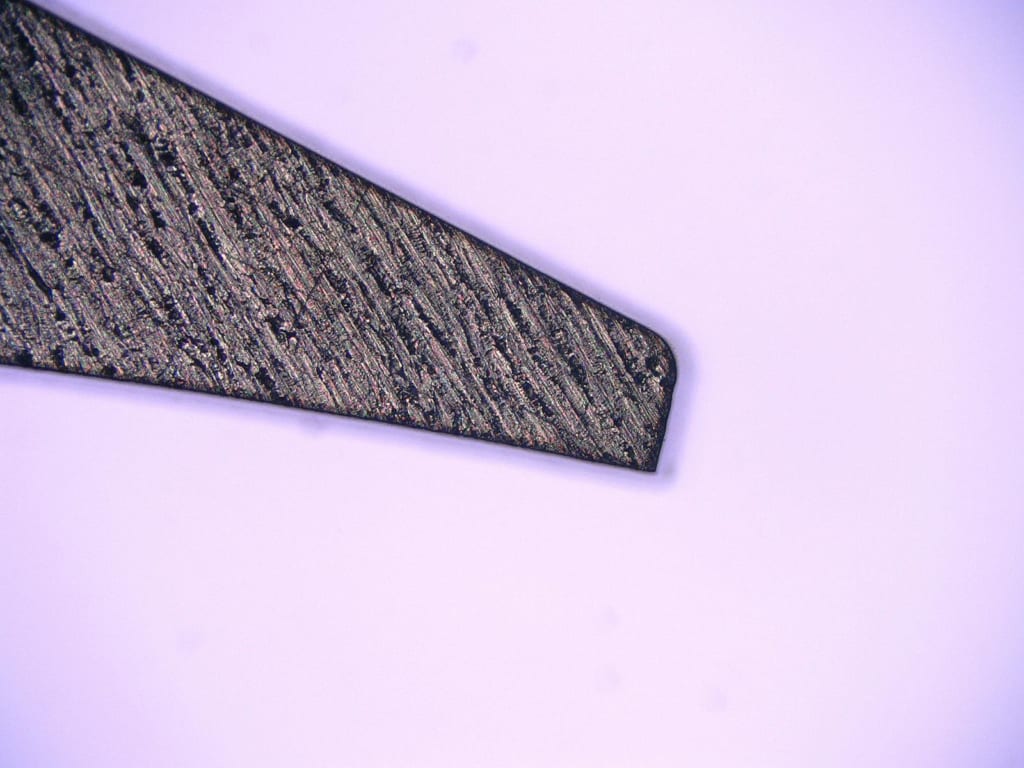
レーザー加工機の駆動系部にリニアを搭載する事によって、以前のボールねじ駆動方式レーザー加工機の苦手とした、角部分の”溶け”の発生を軽減できます。
高精度加工レーザーの生産能力を更に向上させる為に加工機の増台にも力を入れており、2020年1月現在、5台のリニア(駆動系)式レーザー加工機を導入しております。
恒温室にて徹底した温度管理
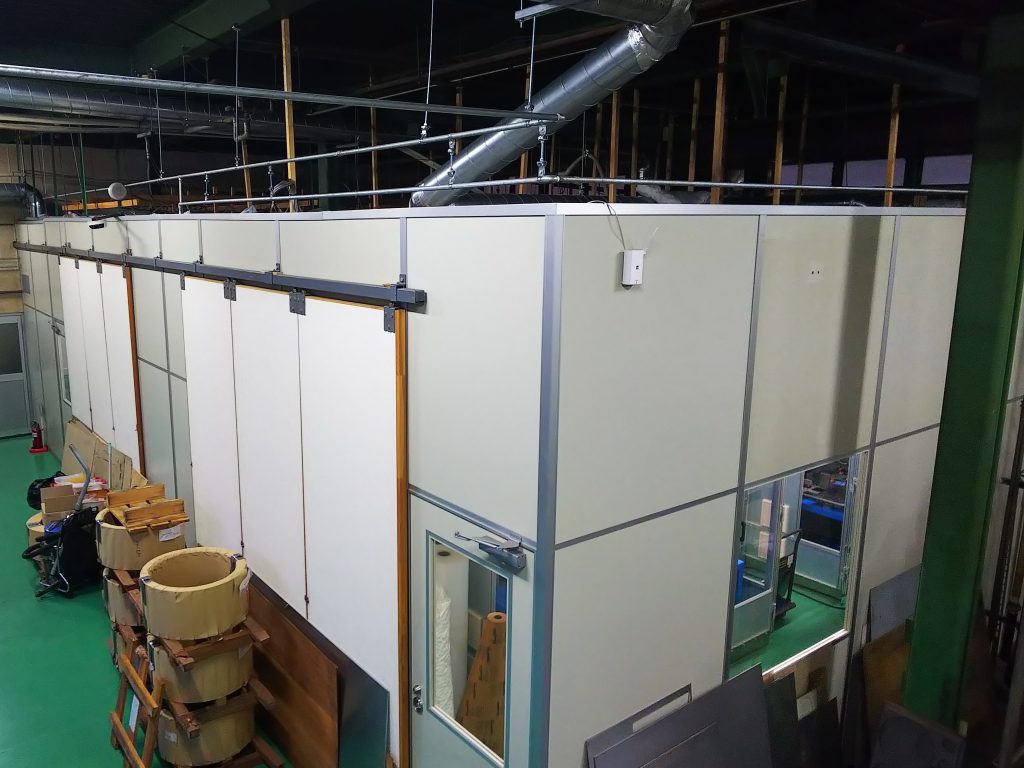
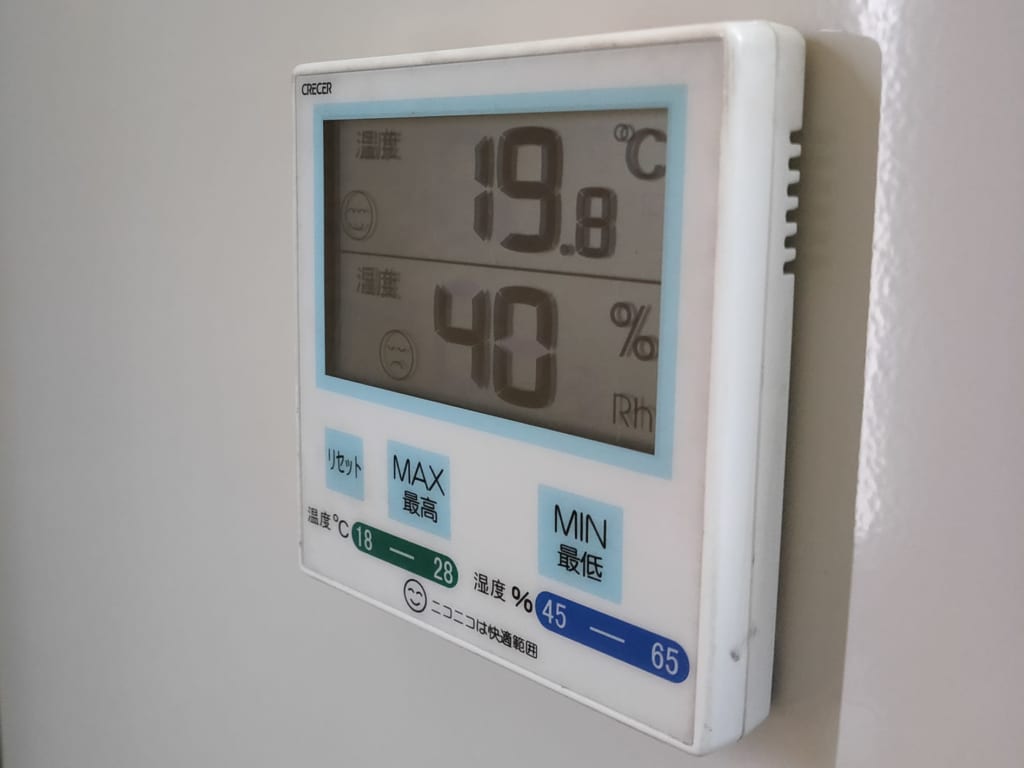
レーザー加工機を小スペースの恒温室内にて運用しており、温度・湿度を一定に保つ事で、精度・加工面粗度により一層こだわった加工が可能です。
ノッチング加工
中型(Φ120)~大型(Φ950)コアの製作
中~大型鉄芯(Φ120~約Φ950)の製作ロット数が増えたときの加工手段として、ノッチングプレス機を導入致しました。
ノッチング加工とは、形状の一部分(主にスロット部)のみの金型を製作し、割り出し盤にて繰り返しプレス加工することで全形状を加工する方法です。これにより金型代を抑えることが可能となり、量産試作レベルのご依頼においてトータルコストを低くすることができます。
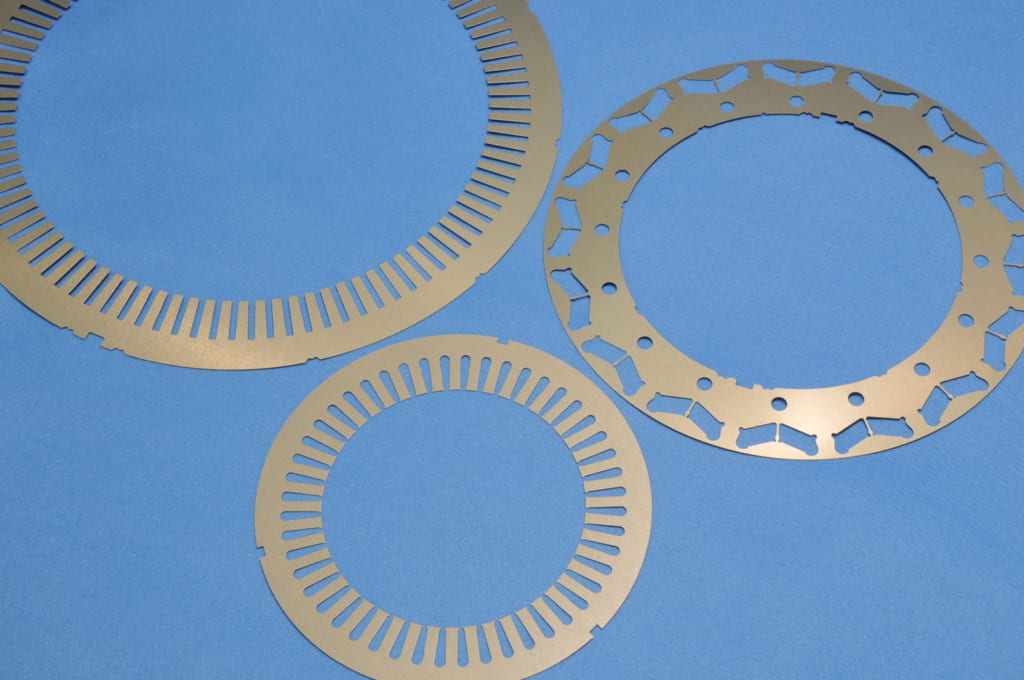
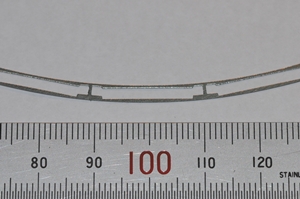
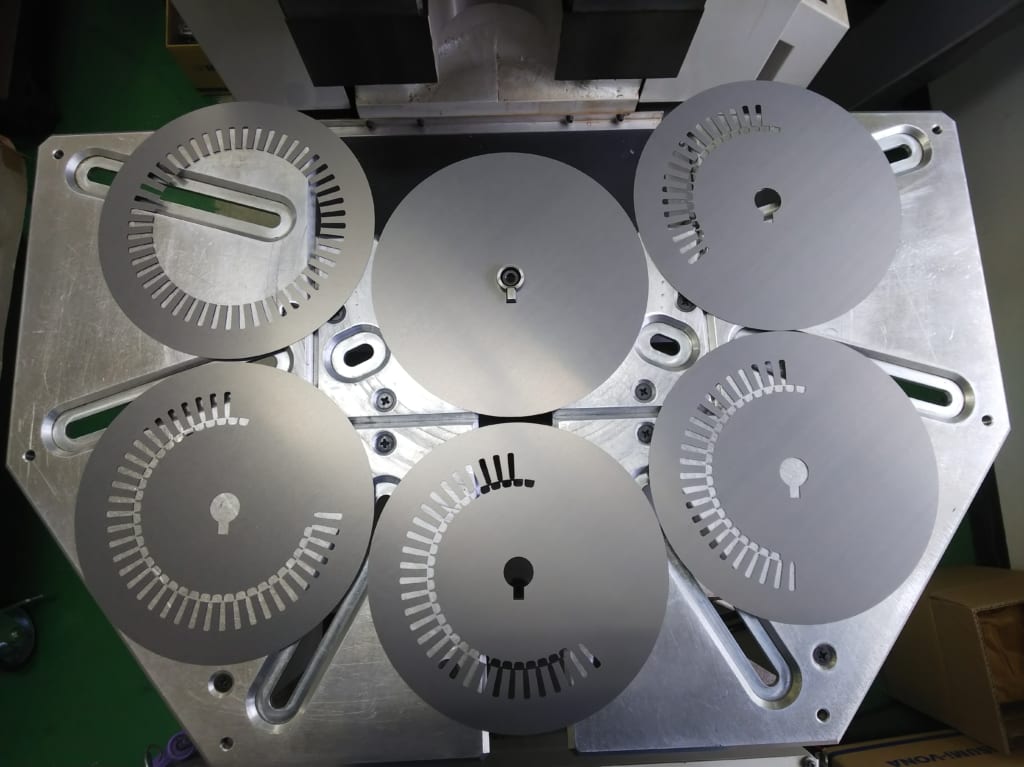
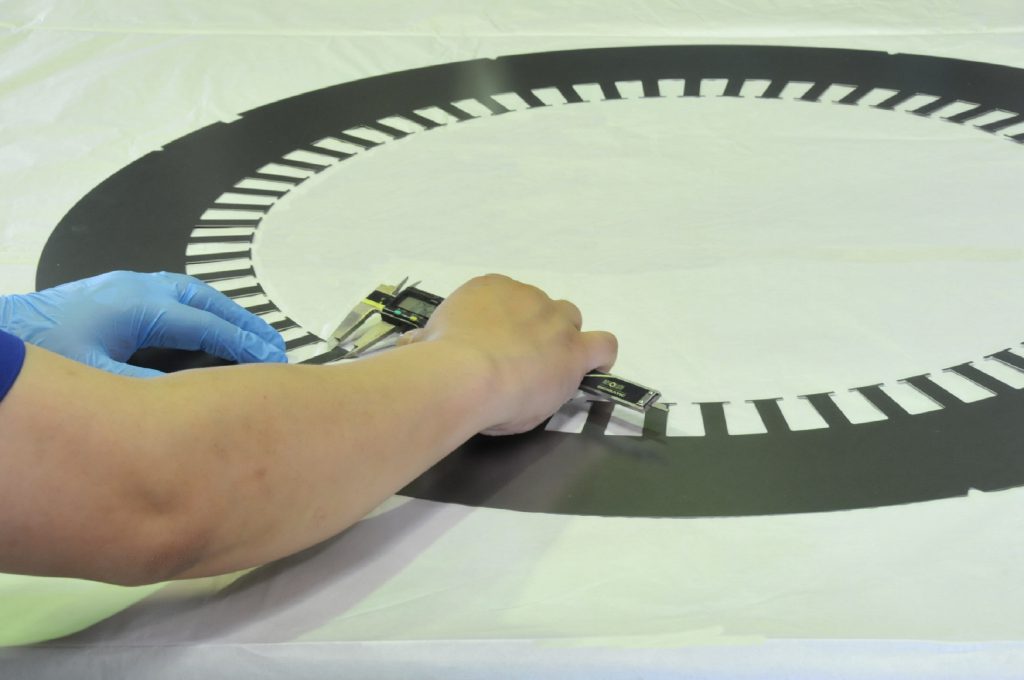
弊社のレーザー加工技術と金型技術を組み合わせる事で、最大径950mmまでの大型コアの試作も行っており、低コスト・高品質でお応えします。
ワイヤー加工
精度・断面重視の加工
高精度の加工はもちろんですが、レーザー品・プレス品との決定的違いはその切断面です。これによりコア特性の向上が期待できます。また、薄板を積層枚数重ねて一気に加工することができ、積層時のズレを極限まで抑えられます。
製品によっては積層治具を必要とせずワイヤ加工後そのままの状態で溶接することも可能ですので、接着積層コアなら接着後の追加工も可能です。
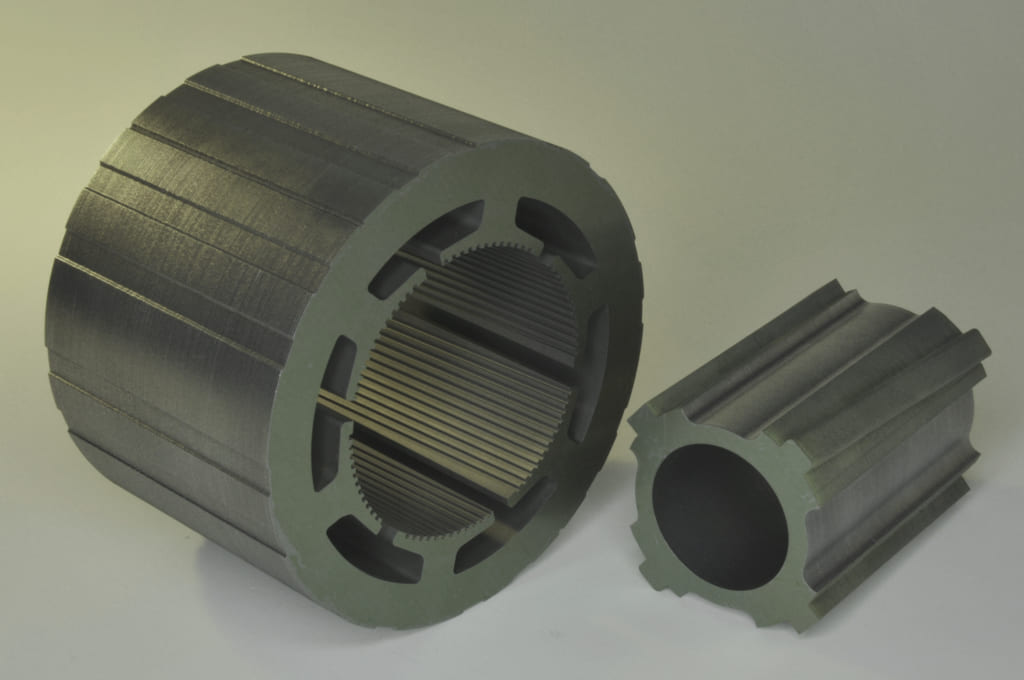
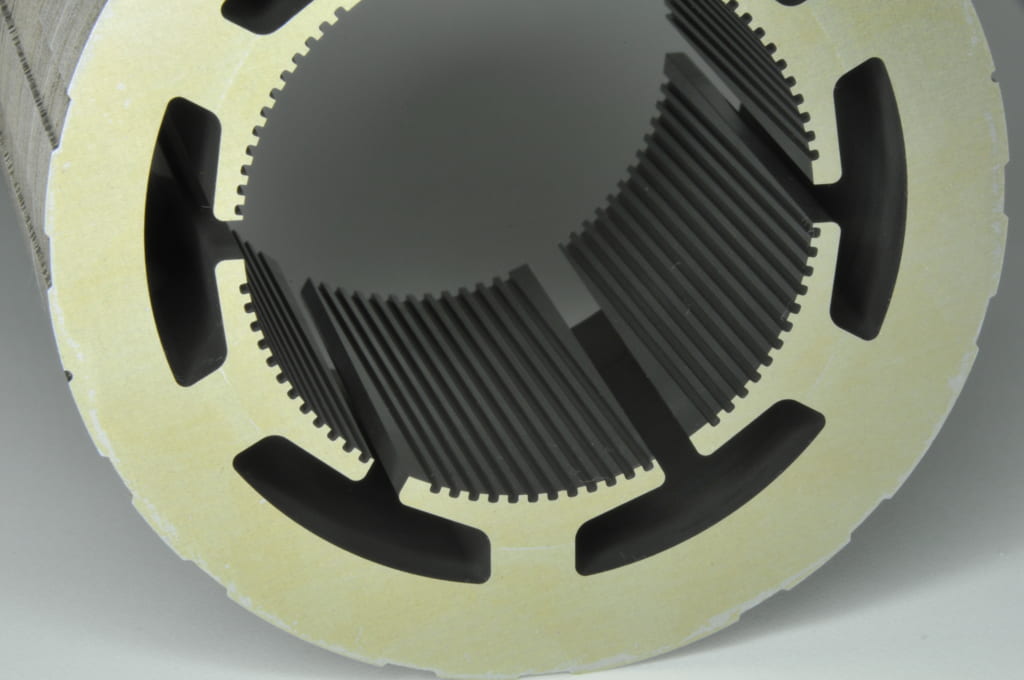
レーザー加工、接着積層後にワイヤー放電加工(スロット部分)
プレス加工
量産試作・小規模ロット量産にも対応
弊社のプレス金型部門では、長年にわたり薄板打ち抜き金型を主に製作して参りました。その技術をモーターコアの試作に活かした自社製金型によるプレス加工により、まとまったロット数の量産試作にも品質とコストパフォーマンスでお応えします。特にφ30以下のコアであれば独自の方法により短納期で製作いたします。
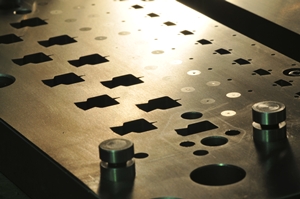
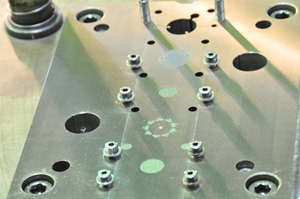